What’s new for CAN in 2017?
News
CAN CiA’s SPS demo highlighted speed advantage of CANopen FD
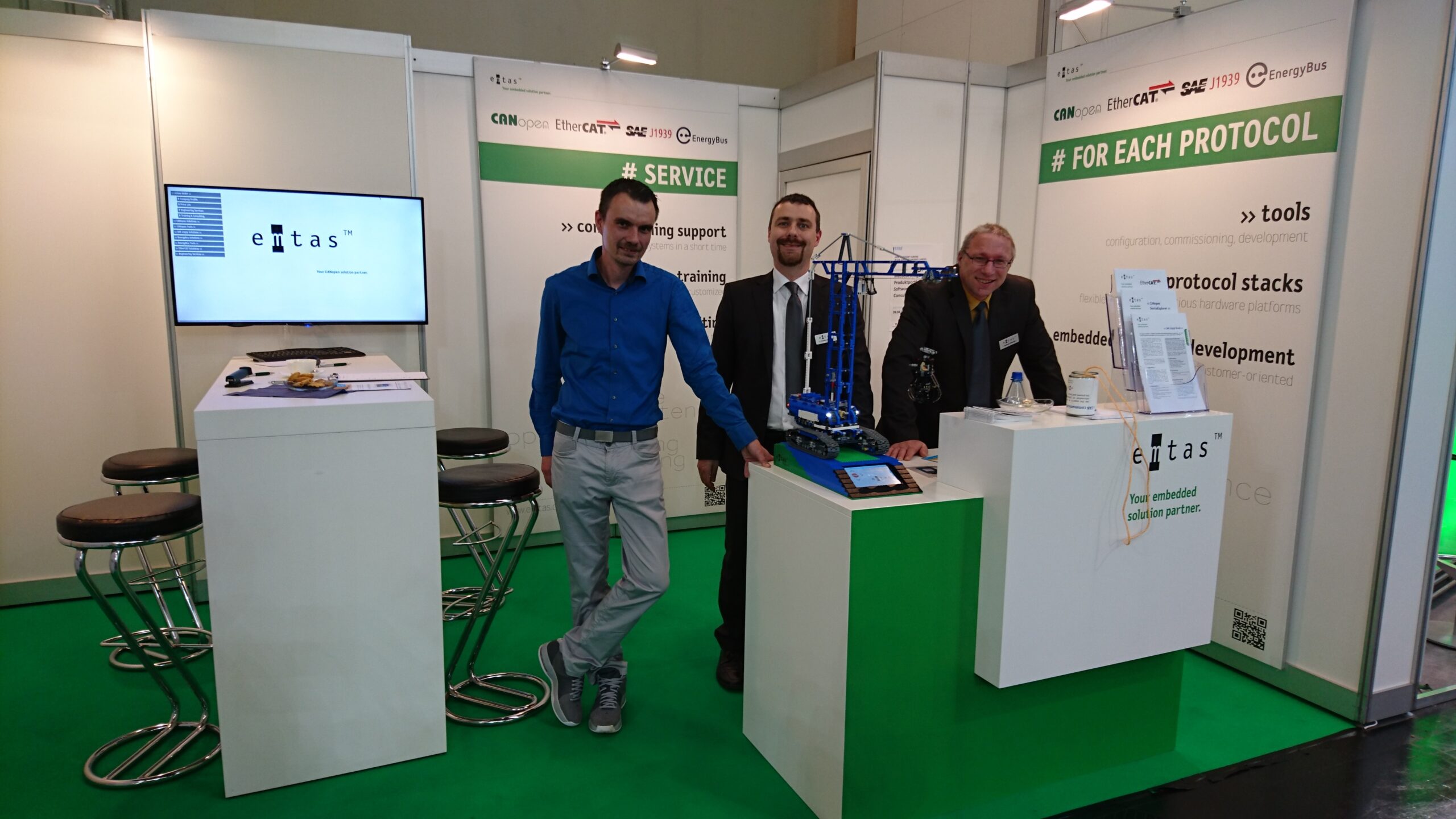
First up is likely to be CAN in Automation’s release of the CANopen FD specification (CiA 301 version 5.0), which is due imminently. First implementations were shown at the SPS IPC Drives tradeshow in November 2016, highlighting the potential speed advantages of CANopen FD. Visitors to CAN in Automation’s (CAN CiA) booth at SPS in Nuremberg had a chance to view CANopen FD in action, thanks to Kvaser’s technical associate partner, EMTAS, and other CiA members, Microcontrol, esd and HMS.
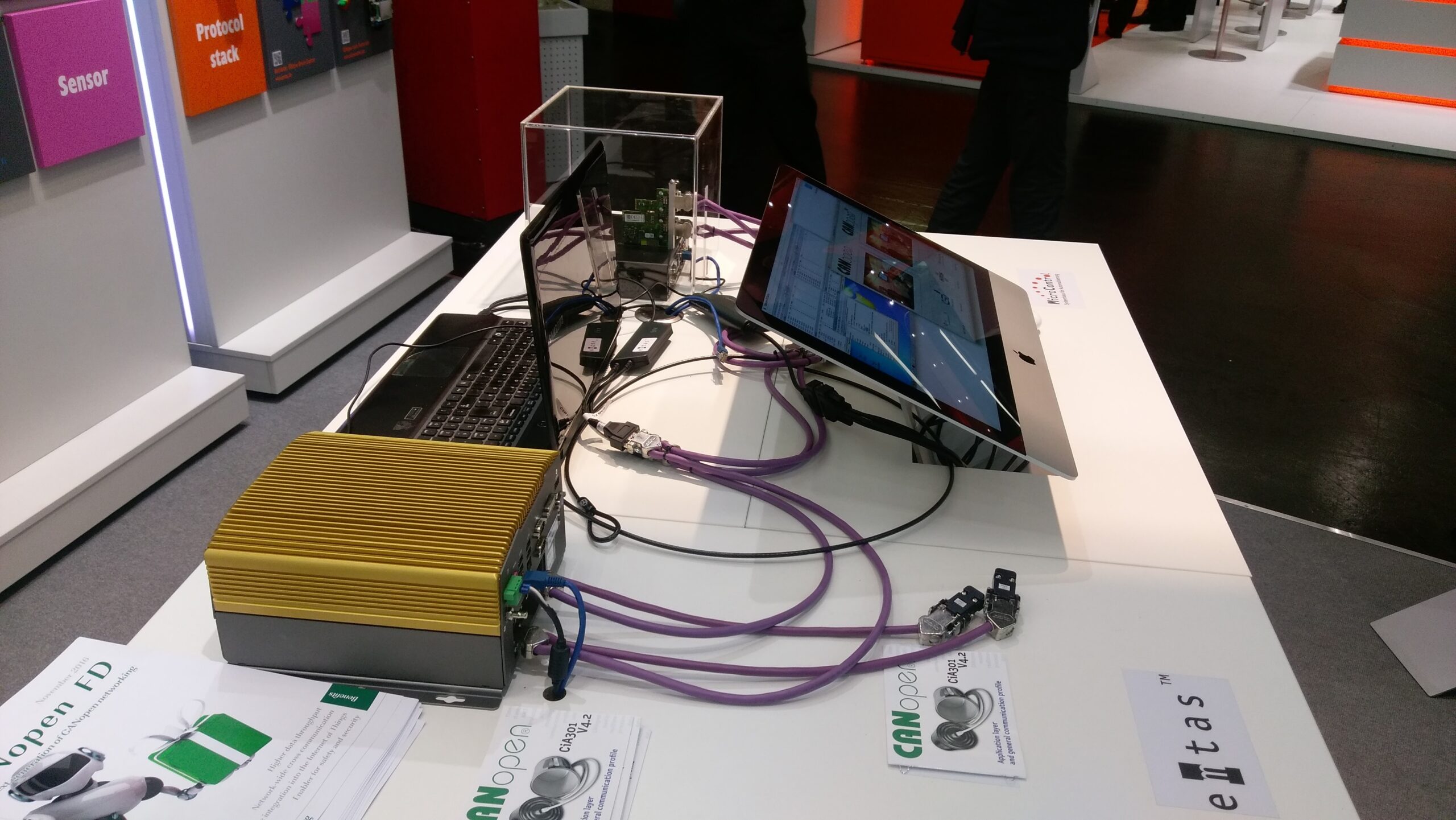
A side-by-side demo was set up to transfer the same image to a server via classical CAN/CANopen and CAN FD/ CANopen FD, with image transfers starting simultaneously. The classical CAN demo (shown below on the left) ran on 500kBit, whilst the CAN FD demo ran at 500kBit in the arbitration phase and 2MBit in the data phase.
The goal of the project was three-fold: to demonstrate the speed advantage of moving to CAN FD, to test CANopen FD prototype integrations from the four companies, and to test the new communication object (USDO) developed by the CANopen SIG Application Layer. “Our own test results suggest that the USDO in CANopen FD is at least six to eight times faster than the classical version,” said Alexander Philipp, who oversaw EMTAS’ involvement.
EMTAS used a Kvaser USBcan Pro 2xHS v2 and Kvaser Memorator Pro 5xHS to connect to the demo. Commented Philipp: “I used Kvaser CAN FD interfaces because we were provided with them from the early days of CAN FD. As a result, we already had a lot of software running with CAN FD from Kvaser, like our CANopen Device Explorer, a CANopen master tool, and our CAN Interpreter analyser.”
Asked about interest in CAN FD at SPS, Philipp notes: “We have been talking about CAN FD / CANopen FD for years, but this time, people coming to the booth said that they are involved in CAN FD projects and want to do CANopen FD. Many of them are designing the whole system or machine and a lot are doing automotive-related development, not the car itself but more on the manufacturing side.”
For more information on the demo, visit CAN CiA or view EMTAS’ YouTube video.
Find out more about Kvaser’s CAN FD interface and datalogging portfolio here.