The CAN Calibration Protocol (CCP) and Universal Measurement and Calibration Protocol (XCP) protocols for reading measurement data and writing parameters to electronic control units (ECUs) are now commonly used during development, testing and in-vehicle calibration. Developed by the Association for Standardization of Automation and Measuring Systems (ASAM), CCP was designed purely for CAN networking applications, whilst its successor, XCP โ introduced in the early 2000s โ caters for a variety of transport layers, including LIN, FlexRay, Ethernet and, of course, CAN. As with any standard, it is impossible to specify every detail for every application, so experienced, trustworthy suppliers are essential to delivering robust solutions.
News
Tailored CCP/XCP solutions for unique customer implementations
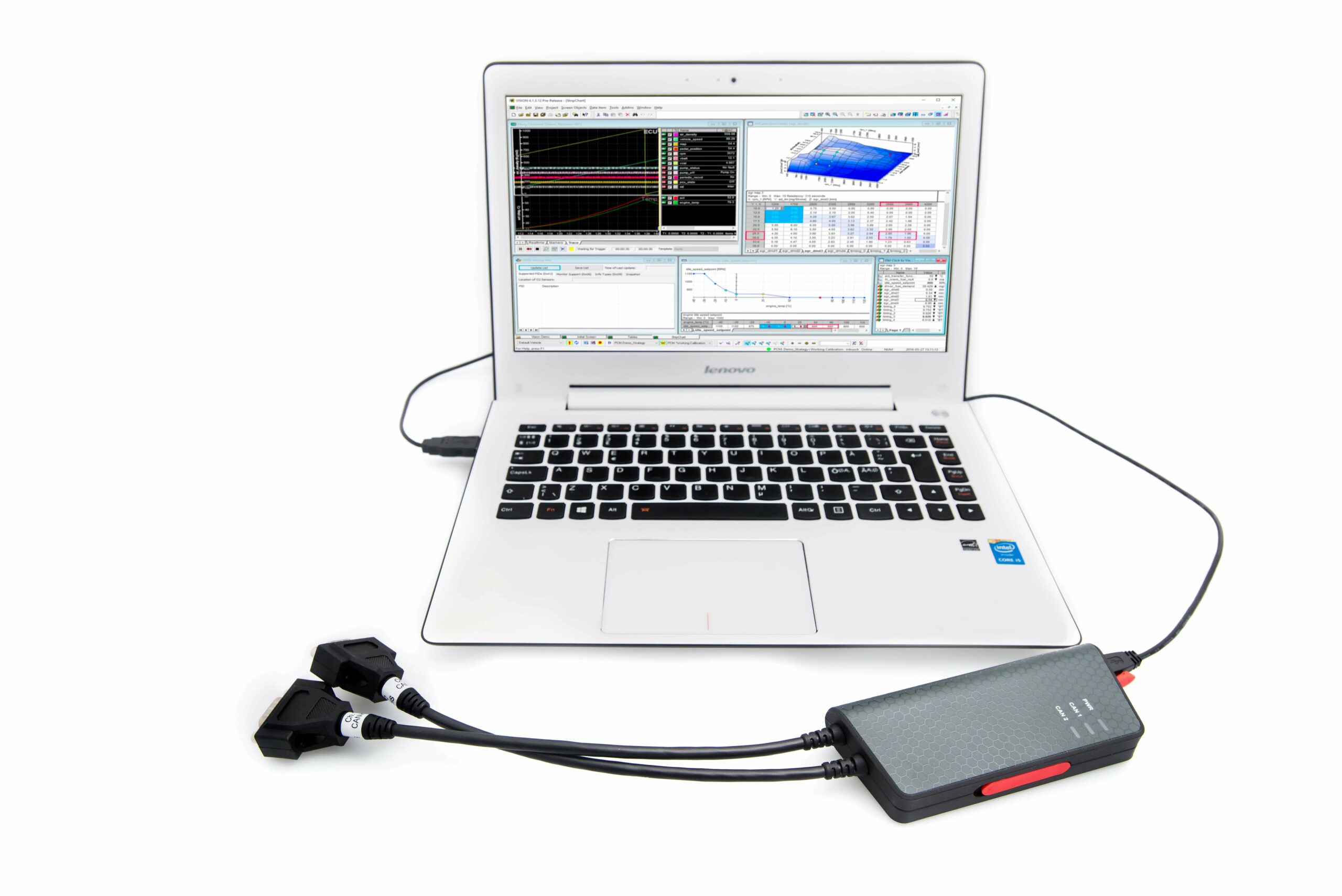
Whilst the CCP and XCP higher layer protocols were intended as universal standards, many vehicle OEMs have implemented them in slightly different ways. A notable example is ECU security, where proprietary usage is not standard and yet is increasingly necessary. For software tool providers, a tailor-made approach โ demanding considerable cooperation between the software vendor and the customer โ is usually required to optimise the calibration toolchain.
Maintaining a secure toolchain
Martin Sventรฉn, Business Manager at Accurate Technologies (ATI) Sweden AB, a Kvaser technical associate, notes: โWhilst some development ECUs are unprotected, most are secured by a proprietary SEEDnKEY mechanism that the development tools need to verify or implement. Access to these security mechanisms demands considerable trust between tool supplier and end customer.โ He adds: โATIโs VISION Calibration and Data Acquisition software has been capable of running CCP/XCP for many years and ATI provides the calibration toolchain for some of the worldโs largest automotive manufacturers. Our engineers are highly experienced when it comes to working with customers to enhance their calibration and measurement process, whilst safeguarding the NDAs and legal protection rightly attributed to modern ECUs.โ
Accurate Technologies often specifies Kvaser Memorator or Kvaser Eagle as the hardware interface between the ECUs and ATI VISION. Kvaserโs single and multichannel products provide the reliability and bandwidth necessary for all CAN-based CCP and XCP applications. In particular, Kvaserโs multichannel interfaces facilitate the handling of data channels from multiple ECUs by time synchronising the data transmitted and received across different buses.
Encrypted t programs
Kvaserโs Memorator product platform is programmable via Kvaserโs t programming language, facilitating a โtailor-madeโ approach to CCP/XCP. Kvaser Memorator customers have the option of implementing an encryption program to protect their intellectual property, in addition to locking the execution of a t program to the Memorator deviceโs serial number. This is how ATI protects customersโ CCP/XCP solutions, including the Seed and Key parameters.
A calibration toolchain needs to be secure, efficient and flexible to meet the increasing complexity of the job. Confirms Sventรฉn: โATI VISION was designed from the outset to adapt to the needs of individual calibrators, making the most common tasks as efficient as possible. Whether it is data acquisition, calibration, rapid prototyping or flashing that customers are doing over CCP or XCP, the combination of ATIโs deep calibration expertise and Kvaserโs trusted CAN interfaces make for a unique partnership that our automotive customers can rely on.โ
For more information on CCP/XCP, please visit www.kvaser.com/ccpxcp/
For a detailed explanation of the difference between CCP and XCP, please visit โThe Move from ASAM CCP to XCP Communication Protocolโ whitepaper.