Aerospace
The aerospace industry was relatively quick to recognise the controller area network’s (CAN’s) inherent reliability. Designed for safety critical systems within the automotive industry, CAN characteristics like a data rate that’s adequate for most real-time control systems, fault confinement and the lack of overhead necessary for bus arbitration make it applicable for aircraft engine control systems, navigation systems and flight-state sensors alike.
Kvaser’s high-speed CAN interfaces are compatible with ARINC Specification 825, the general CAN standard for airborne use, as well as J1939, CANopen and DeviceNet.
The ARINC 825 specification is based on the use of 29-bit identifiers, which are supported by all Kvaser interfaces, meaning that they can transmit and receive all ARINC 825 CAN-frames perfectly. Kvaser’s CANlib driver for Windows and Linux will send and receive any CAN-frame – it is up to the application layer software to ensure that the CAN-frames being sent are configured according to ARINC 825.
One issue concerning ARINC 825, when using a PC running Windows or Linux, is the timing delay when sending CAN-messages. ARINC 825 has “Time Triggered Bus Scheduling” rules that set real-time constraints. In order to comply with these, Windows and Linux are not the best choice of operating system, though if your Windows computer is high enough performance, it may be possible to use it without causing problems in the ARINC 825 communication. The challenge is to guarantee performance in all conditions over a long period of time.
A means of addressing the timing issues posed by ARINC 825 would be to employ the Kvaser Memorator Pro 2xHS v2 CAN to USB high-speed interface and data logger, which is capable of running user-developed t scripts. The Kvaser Memorator Pro’s simple-to-develop scripting language can be used to create a CAN transmission schedule that would allow users to load values to be transmitted through the PC, when the Kvaser Memorator Pro is in interface mode, as well as check whether other modules are meeting ARINC 825’s timing requirements.
Another solution to ARINC 825’s timing rules would be to choose a real time operating system (RTOS) to use with Kvaser’s hardware. At present, Kvaser does not provide RTOS drivers (as there’s too wide a selection to keep maintained and up-to-date), but we recommend that you contact one of our Technical Associates that specialise in RTOS drivers (see recommended Associates below, or the full list here). Alternatively, users can elect to write their own driver for our hardware using the source code from Kvaser’s Linux driver as a guide.
Related Articles
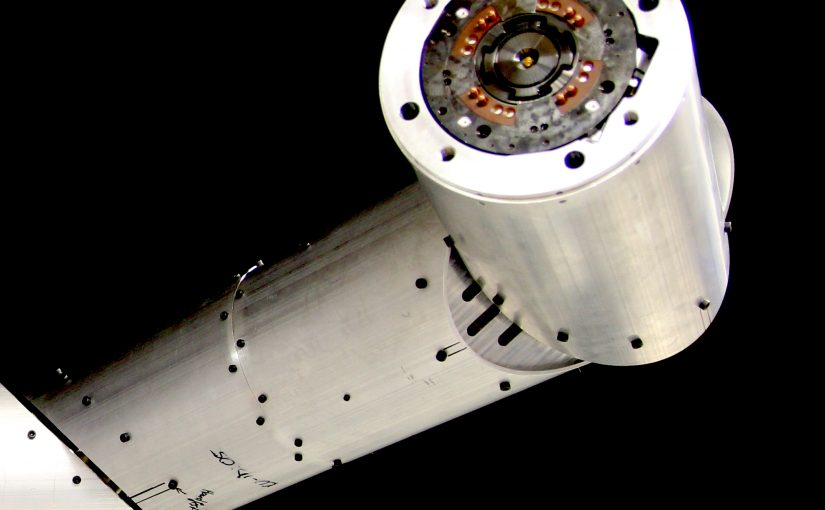