Hydromotion, formally, TU Delft Hydromotion team, is a team of ambitious students, who, every year, build some of the most advanced boats on earth. Driven by their desire to see wider adoption of sustainable fuels, the team hopes to inspire the greater maritime industry to follow suit. Previously, the team was called TU Delft Solar Boat Team, as creating Solar Boats were the main focus but with hydrogen’s myriad advantages over solar and battery electric in open-sea vessels, the switch to hydrogen was made. The team has been designing, producing and racing these boats since 2006, and created ‘The World’s First Flying Hydrogen Boat’ in 2021.
News
Hydromotion creates ‘The World’s First Flying Hydrogen Boat’ ahead of Monaco Energy Boat Challenge
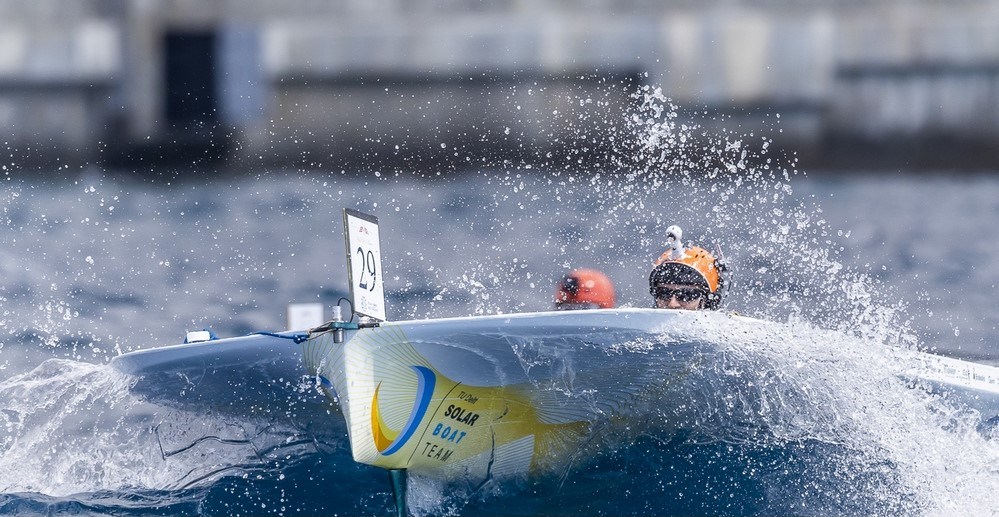
The team is comprised of students from various backgrounds, ranging from Applied Mathematics and Physics, to Molecular Science and Technology, as a wide range of expertise is needed. Even with their varying expertise, the students work with industry experts and alumni to optimize as much of the project as possible. Two notable industry experts are Kvaser and ODOS, which have supplied CAN equipment and Cloud platform to the team.
Most devices on the boat communicate using the CAN protocol, including the inertial measurement unit, ultrasonic height sensor, height control, dashboard, energy management systems, fuel cell, motor controller, wing actuators and steering wheel. Currently, the team uses a mix of Kvaser Leaf Lights and Kvaser U100 CAN interfaces to test, develop, and monitor the CAN interaction between the different CAN devices on the vessel. Kvaser’s CAN interfaces are paramount to the development of the boat, as they not only streamline the CAN communication development process, but help the team understand exactly how the devices interact.

Hydromotion’s boats contain many CAN devices that must communicate, and for many purposes, that data should be recorded. The team were wary of some traditional data loggers on the market, which have proprietary formats and software. Having used various data logging solutions in the past, from a custom one, to a not particularly flexible commercial one, they were keen to try a different approach.
To meet the challenges of this marine safety critical application, the Hydromotion team implemented a redundancy data acquisition system, consisting of local and remote datalogging techniques:

- A local hardwired Kvaser Memorator 2xHS v2 datalogger for tuning fail safe systems, such as active height control, and storing CAN data locally on SD card for the boat crew to access.
- This shall be used in parallel with a remote wireless ODOS’ CloudCommander 4G CANbus-to-Cloud gateway, dashboard and cloud platform for live data monitoring, analysis and visualisation by distributed onshore support team, and remote data storage with redundancy backup in the event of local SD card failure.
Although the implementation of everything ODOS does is closed sourced, it appears to follow the open-closed principle, in that everything is closed for modification, yet open for extension. This principle is carried forward in the execution of the data logging and viewing. To log data from the CAN protocol, the user simply has to provide the logger with a standard database file that represents their system. The data is then sent to a server hosted by ODOS, with zero user intervention. Data can be viewed from a highly customizable CloudSoft Dashboard that ODOS provides. However, users can and are encouraged to create their own front-end webpage, using an exposed REST API.
“This is exactly what Hydromotion needed from data acquisition, as the data can be viewed for real-time statistics, analysed later for performance retrospectives, and shared live for follower interactions.”
Note: At the time of writing, Hydromotion’s 2022 boat hasn’t yet sailed yet, so the team have only briefly used the ODOS and Kvaser data loggers. However, the boat will sail for the first time in mid to late April, ‘flying’ about two weeks later, in preparation for the biggest event of the year, the Monaco Energy Boat Challenge, in July. A follow-up article later this year will describe how the team got on.